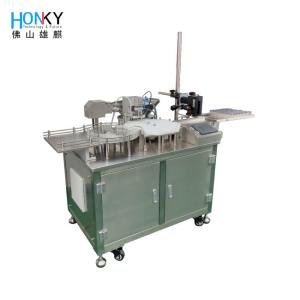
Add to Cart
Automatic small size forzen dry liquid vial filling machine with plug adding automatic for frozen dry pre-filling using
Characteristic of Automatic small size forzen dry liquid vial filling machine
Expanded Description of XQXL-3C Automatic Small Size Frozen Dry Liquid Vial Filling Machine
The XQXL-3C Automatic Small Size Frozen Dry Liquid Vial Filling Machine utilizes a desktop filling and capping design, which is specially crafted to efficiently fill and cap penicillin bottles. The filling pump of this machine incorporates a high-precision ceramic pump to guarantee the utmost accuracy in filling, ensuring that each vial contains the precise amount of liquid required.
The machine's appearance adopts a sleek and compact desktop design, making it an ideal choice for laboratories and production environments with limited space. Its small size not only saves valuable workspace but also allows for easy maneuverability and positioning. Furthermore, the machine is constructed from high-quality 304 stainless steel, which is renowned for its corrosion resistance, durability, and ease of cleaning. This material choice ensures that the machine maintains a high level of hygiene and complies with industry standards for medical equipment.
In terms of productivity, the XQXL-3C boasts an impressive filling speed of up to 1800 bottles per hour, making it an efficient solution for large-scale production needs. After the filling process is completed, the machine is equipped with a code printing function, which allows for the automatic application of unique codes or batch numbers to each vial. This feature enhances traceability and ensures that each vial can be easily identified and tracked throughout the production and distribution process.
Primarily, this machine is designed for the frozen-dry powder pre-filling work, where it plays a crucial role in the preparation of vials containing frozen-dried powder for later reconstitution. With its combination of precision, efficiency, and ease of use, the XQXL-3C Automatic Small Size Frozen Dry Liquid Vial Filling Machine is an invaluable asset for any medical or pharmaceutical manufacturing facility.
Technical data of Automatic small size forzen dry liquid vial filling machine
Model | XQXL-3C |
Pump type | Ceramic pump |
Filling accuracy | ≦±0.5% |
Filling range | 0.6-6ml |
Manufacturing speed | 25-30 PCS / minute |
Power | AC 220V 50-60Hz 550W |
Air pressure | 0.4-0.6Mpa |
Machine size | 1500*850*750mm (Main machine roughly) |
Machine display of Automatic small size forzen dry liquid vial filling machine
This equipment has been tested to meet the requirements of GMP certification.
The separation part adopts high purity ceramic pump, which controls the injection volume of each lap by adjusting the angle of the pump head, and has extremely high measuring accuracy and repeated consistency.
Fully desktop design to make operation easy and with the date printing function.
Advantages for using the ceramic pump:
1. Low Friction, Increased Packing Life
2. Extreme Wear Resistance
3. Increased Corrosion Resistance
4. Improved Anti-Galling Surface
Application area
1. ODM and OEM products design;
2. Automatic manufacturing line design;
3. Cosmetic product packing;
4. Pharmaceutical and bio-reagent product packing;
5. Laboratory Liquid dispensing;
6. Lithium Battery Liquid dispensing;
7. Ceramic pump and ceramic pump part design;
8. Other area's material filling;
Q & A
Q: Do you offer OEM services, I am a distributor from overseas?
A: Yes, we can offer both OEM Services and technical support. Welcome to start your OEM business.
Q: How about the after-sales service?
A: The machine is a 1-year warranty. And we offer lifetime after-sale service and technical support.
Q: What are your Installation Services?
A: Installation Services are available with all new machine purchases. We will provide the user manual and videos to support installing, debugging, operation of the machine, which will indicate to you how to use this machine well.
Q: What info will be needed to confirm machine models?
A: 1.The material status.
2. Filling range.
3. Manufacturing speed.
4. Requirements for the production process.